Supply Chain
102-9Metalloinvest’s supply chain management system reflects the entire movement of materials within the Company’s production processes and includes the procurement of materials, their use in production, product creation, marketing, and logistics.
Procurement activities are a strategic component of Metalloinvest’s supply chain management system. Procurement management is handled by the Supply Directorate and is governed by the Company’s Procurement Policy.
At present, procurement activities are undergoing a stage of active transformation in order to ensure a full transition from a support function to a strategic function.
Role of the procurement function:
- determining the need for material resources;
- searching for and selecting suppliers;
- concluding contracts and monitoring their fulfilment;
- obtaining the material resources. Processing incoming flows of material resources, identifying products, clarifying quantity, preparing reports, and transferring the raw materials to the place of their use and storage
- checking incoming products and confirm quality.
The department’s key functions include:
- creating added value through cross-functional interaction;
- optimising procurement procedures, which significantly affects business efficiency indicators;
- impacting the business environment through interaction with suppliers and finding mutually beneficial positions.
In order to ensure the sustainability of procurement activities, the Company adheres to the following principles:
- transparency;
- hiring of local suppliers;
- priority of procurements from manufacturers and their legal representatives;
- diversification of procurement channels;
- focus on building long-term relationships with suppliers;
- continuous quality control of purchased goods and services.
Total procurements by the Company’s core enterprises amounted to RUB 195 billion in 2018.
Except intragroup procurements from Lebedinsky GOK, OEMK, Mikhailovsky GOK, Ural Steel, Holding Company Metalloinvest, Management Company Metalloinvest, and Metalloinvestleasing.
Interaction with local suppliers
204-1
Metalloinvest continued to focus on procurements from domestic manufacturers in 2018. The share of Russian suppliers remained high at 93%*. Materials that are not produced on the Russian market were imported.
* Russian procurements include all purchases made within Russian borders. This value excludes procurements from Russian manufacturers in foreign countries with production facilities outside the borders of the Russian Federation.
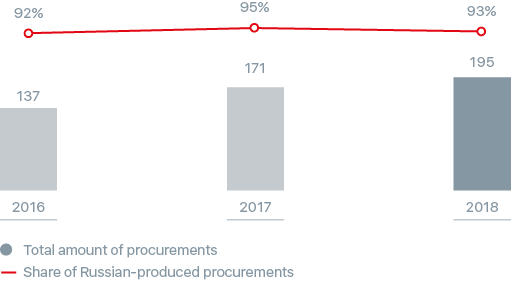
As part of the overall corporate transformation carried out at the Company, one of the objectives that was set during the reporting period was to introduce an effective operating model for procurements in order to streamline the process and to also ensure that the changes in the operating model are consistent with the project to introduce SAP.
The extensive preparatory work carried out over the first quarter of 2018, which included the development of a roadmap and seminars for employees of the procurement unit, resulted in the introduction of a new operating model at all of the Company’s plants in autumn 2018. The new model involves spinning off systematic category management practices as well as a clear division of functions, which helps to considerably simplify and speed up procurement processes.
In addition, procurements of work and services were centralised for the needs of the plants. This process has led to the following key results:
- a reduction in costs by consolidating demand;
- increased transparency due to unified procurement procedures;
- the formation of category strategies and a focus on strategic categories of services.
As part of the procurement process, Metalloinvest has expanded the use of electronic trading platforms (ETP), which has made it possible to increase the transparency of procurements and ensure a transition to unified interaction with all suppliers. A total of RUB 5.6 billion worth of procurements were transferred to the electronic process in 2018.
The Company continued to transition to the automation of the procurement process during the reporting period in accordance with its policy on digitisation and the introduction of the SAP system: individual procurement steps were automated to ensure their unification, improve control procedures, and minimise errors.
Transformation of the procurement operating model
The new procurement operating model that has been introduced at all Metalloinvest enterprises divides procurement activities into three main functions.
- Front office. The front office’s key tasks include category management of procurements, including the development and implementation of a category strategy, as well as strategically managing the provision of materials by specific groups, including the selection of partners for long-term contracts.
- Middle office. The middle office is in charge of operational procurements. Middle office employees study the Company’s current procurement needs, determine the best procurement channels, and coordinate the sources of supply.
- Back office. The back office performs a supporting role: it drafts contracts and specifications, monitors and controls the execution of transactions, organises transport support, and monitors the receipt of products and their payment.
In addition, each enterprise has set up methodological support and procurement development services that are tasked with identifying ways to improve and implement procurement activities, drafting and updating regulatory documents, and providing technical support when working with information systems.
Accounting support for procurement activities (sending and receiving contracts as well as accepting and recording primary documents) was spun off into a separate function and transferred to be managed by the multifunctional shared services centre (MF SSC).
The transformation has resulted in a transition from a reactive procurement management system that involved carrying out procurements for specific tasks, long periods of bidding and signing contracts as well as one specialist performing the entire range of functional tasks to a unified end-to-end process. The transformation has created the following advantages:
- the creation of an organised structure that ensures the rapid development of the function and allows for swift changes;
- enhanced transparency of the procurement process;
- the ability to effectively forecast the Company’s needs.
Plans for 2019:
In 2019, Metalloinvest plans to:
- optimise processes within each of the functional units that have been spun off;
- continue developing category management through effective work by cross-functional teams;
- standardise requirements for category strategies;
- introduce cross-functional analytical reporting;
- introduce a differentiated approach to supplier management.
Automation of the procurement process: results of 2018
Metalloinvest introduced a number of automated tools in 2018, including:
- Automatic generator of tender forms, which helps to streamline the work of employees for a group of operational procurements
- Automatic generator of specifications – a handy tool for specialists as part of contractual work
- Tool for automatic distribution from the monitoring registry, which helps to streamline the monitoring process and make interaction with suppliers more efficient
- Automatic generator of contracts with suppliers that are residents of the Russian Federation with the ability to add specific provisions, which significantly speeds up the process of negotiating contracts
- A tool for interaction between supply service employees and suppliers to track the operational procurement process, exchange information quickly, and collect information about procurements that have been completed
- Dynamic analytical reports based on data obtained from the system of employee interaction. This tool helps to track the day-to-day activities of departments, identify delays in work, and take corrective measures.
Principles of interaction with suppliers
102-43
Metalloinvest is guided by the principles of transparency and equal opportunity when it selects suppliers. In addition to conventional criteria for selecting suppliers, such as price, the quality of products and services, supplier reliability, and delivery time, the Company takes into account the adaptability of manufacturing processes, including for eco-friendly production, and also takes into account the willingness of suppliers to strictly adhere to the principles of business ethics and human rights. Standard contracts with suppliers include an anti-corruption clause, which states that Metalloinvest’s suppliers agree to combat corruption. Any violation of these obligations results in the termination of business relations.
Key mechanisms for interaction with suppliers:
- verification of suppliers to confirm their reliability;
- interaction with potential suppliers within commercial negotiations;
- interaction with suppliers to improve the economic conditions of agreements with core suppliers.
In 2019, the Company plans to further stabilise interaction with suppliers by introducing a survey of the parties involved in the tender process with questions about whether potential business partners have appropriate social and environmental policies and practices.