Emissions, Air Protection and Climate Strategy
Air protection is a major priority for the Company in terms of environmental protection. The Company is implementing a number of initiatives that aim to stabilise the amount of pollutant and dust emissions as it significantly expands production.
305-7
Total air emissions totalled 116,600 tonnes in 2018, an increase of 3% from the previous year due to the Company’s expanded production capacity. Dust control initiatives that were implemented during the reporting period, including retrofitting (for more details, see the section Key air protection measures), helped to reduce the amount of solid particles emitted into the atmosphere by 4%.
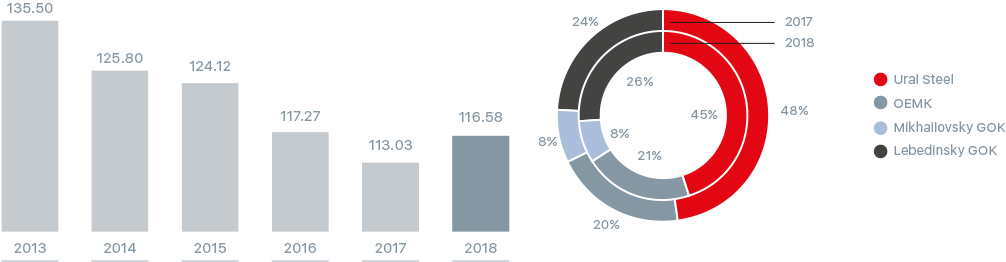
2016 | 2017 | 2018 | |
---|---|---|---|
Particulates | 18.3 | 17.3 | 16.6 |
Gaseous, including | 98.9 | 95.7 | 100.0 |
SO2 | 20.7 | 21.4 | 22.3 |
CO | 60.6 | 57 | 59.8 |
NO2 | 14.4 | 14 | 13.8 |
Other volatile organic compounds | 3.2 | 3.3 | 4.1 |
Total emissions | 117.2 | 113 | 116.6 |
Key air protection measures
The Company implemented a wide range of dust control and air protection initiatives in 2018.
Installation of a suction system in the limestone screening unit at OEMK
The suction system cleans the air of the limestone dust that is generated when it is screened and has treatment efficiency of 99.99%. The installation of the suction system has helped to significantly reduce the amount of fugitive emissions.
Reclamation and greening of industrial sites at Lebedinsky GOK
Metalloinvest carried out biological reclamation work on loose dump pits in 2018 by planting acacia (on an area of 10 hectares) as well as lilac saplings and grass (on an area of 15 hectares). In addition, a forest shelter belt was created along the perimeter of the overburden rock. These measures not only had a positive effect on the region’s biodiversity (for more details, see the section Maintaining Biodiversity), but also helped to reduce dust generation.
In addition to the biological reclamation of rock and loose overburden, Lebedinsky GOK conducted sanitary and hygienic reclamation on dam levees on its territory at a tailings dam using loam (9.3 hectares) and black soil (8.5 hectares) and also washed away temporarily unused compartments of the tailings dam with loam (on an area of 300 hectares). These measures helped to restore disturbed lands (for more details, see the section Maintaining Biodiversity) and also fortified dust-forming surfaces.
Dust control measures using reinforcing solutions at Lebedinsky GOK
The Company continued to implement hydro-mechanical dust control measures using ground-based irrigation equipment and small aircraft. Dust-forming areas of tailings facilities were irrigated with the DUSTBIND acrylate-containing agent using aircraft (616 hectares). In addition, the roads of the mining pit, tailings facilities and crushing and sorting plant were treated with the Bischofite binding agent (Bischofite solution). Both agents stabilise dust-forming surfaces, binding solid particles and preventing surface weathering. These measures have significantly reduced dust generation.
Retrofitting and modernisation of the dust collection system at Mikhailovsky GOK
A major environmental event for Mikhailovsky GOK during the reporting period was the start of the modernisation of the dust collection system at the pellet plant’s open storage facilities, which mainly tranship pellets. This inevitably results in fugitive emissions of dust from bulk materials due to wind exposure. The new dust collection system will significantly reduce dust generation.
Reconstruction of the suction system at Ural Steel
Ural Steel launched a project in 2018 to rebuild the suction system at blast furnace stock houses. The suction system was rebuilt to ensure that the dust concentration after treatment is no more than 20 mg/m3. New bag filters and blower equipment are slated to be installed as part of the renovations. The project will significantly reduce the dust load on the environment.
Plans for 2019
The following goals were set for 2019 in accordance with the short-term environmental goals of the Group’s enterprises:
- reducing dust air pollution due to a decrease in dusty areas at the tailings dam at Lebedinsky GOK;
- reducing emissions of harmful air pollutants by replacing the integrated equipment of the shot-blasting unit, including the suction system at OEMK;
- reducing emissions of harmful air pollutants from emission sources at the blast furnace shop at Ural Steel as a result of the completion of the modernisation of the blast furnace dust collection system.
In the mid term, the Company also plans to equip stationary emissions sources at all plants with automated devices to measure and record pollutant emissions and/or discharges as well as technical equipment to record and transmit information on pollutant emissions and/or discharge indicators.
Managing climate change
Greenhouse gas emissions are primarily generated by burning natural gas and coal when manufacturing steel products, iron, and HBI/DRI at plants in the metallurgical segment.
In this regard, the Company is implementing a number of measures to monitor greenhouse gas emissions, is a member of various industry associations, and supports initiatives to reduce CO2 emissions. Each year, the Company receives a certificate of the international Climate Action programme from the World Steel Association.
Total direct carbon dioxide emissions (scope 1) by the metallurgical sector’s plants totalled 9,091,000 tonnes of CO2 equivalent during the reporting period, up slightly (by 1.5%) from the previous period due to increased production. At the same time, the successful implementation of initiatives to counter climate change has made it possible to significantly reduce (by 21%) specific emissions at Ural Steel and avoid a significant increase at OEMK.
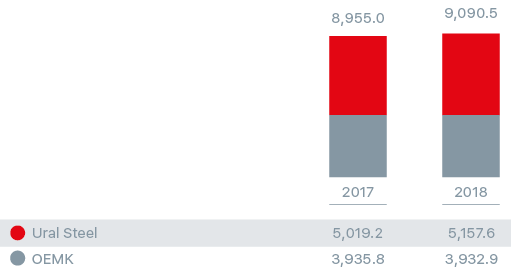
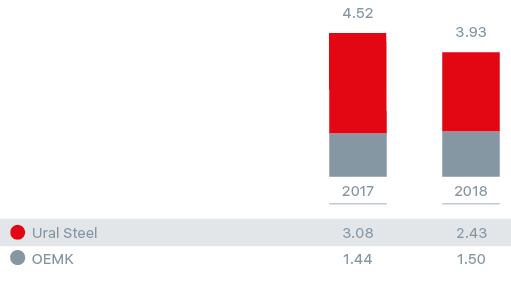
Direct emissions (scope 1) and specific greenhouse gas indicators are calculated in accordance with WSA methodology.
In addition to monitoring emissions at all the holding’s enterprises, the Company plans to devote significant attention to reducing direct greenhouse gas emissions and increasing carbon capture. These measures should help Metalloinvest assess its capabilities for cutting greenhouse gas emissions and set reduction targets by 2021.
Cooperation with the World Steel Association
Metalloinvest is a member of the World Steel Association, which is one of the largest international organisations in the industry and brings together more than 160 global steel companies, as well as national and regional industry associations and research institutes. World Steel Association members collectively account for roughly 85% of global steel production.
Metalloinvest is committed to meeting the highest industry standards and regularly hosts representatives of the association who inspect the Company’s enterprises for compliance with safety and occupational health requirements. The Company began regularly providing the association with quantitative data on environmental and occupational health and safety indicators as well as personnel indicators during the reporting period. In 2019, Metalloinvest also plans to begin providing quantitative indicators for a life cycle assessment of steel products as part of the Life Cycle Assessment initiative. The association will then use this data to conduct research to assess the impact that production processes have on the environment.
A key area of cooperation between Metalloinvest and the World Steel Association is their membership in the Climate Action programme, which is the basis of a global initiative to reduce CO2 emissions in the steel industry. As part of this programme, the Company collects, calculates, and provides data on greenhouse gas emissions generated during production based on the association’s methodology and standards. A comparison of data from the Company’s different enterprises will determine the most effective tools for reducing CO2 emissions.