Occupational Health and Safety
Employee safety remains the Company’s highest priority. Total investments in OHS increased by more than 3% during the reporting period compared with the previous reporting period and enabled the Company to implement a number of measures and integrate advanced technologies into OHS. The Company provides its employees with the highest quality personal protective equipment, which is selected based on multi-stage testing, and its fitness is now monitored automatically using a bar-coding system over the course of its service life. Metalloinvest is continuously searching for optimal solutions in employee safety and encourages continuous interaction in this regard both between enterprises and outside of the holding.

Occupational Health and Safety Management System
403-1
The occupational health and safety management system did not undergo any changes during the reporting period and still encompasses all employees of the holding’s enterprises.
OHS issues are managed both at the level of the Management Company, as represented by the First Deputy CEO - the Chief Operating Officer as well as the Environment, Occupational Health and Safety Division, and at the enterprise level, as represented by chief engineers and heads of specialised departments.
403-4
The Company has had an Environment, Health, and Safety Committee since 2017. The Committee meetings are held on a monthly basis and chaired by the CEO. In addition to the CEO himself, the Committee includes his first deputies, heads of functional units, Company employees, and representatives of all companies under the holding’s management. The Committee’s main function is to make strategic decisions and coordinate the work of the OHS units.
The Company’s working condition requirements are not only determined by Russian legislation, but also by the recommendations of the OHSAS 18001:2007 international management and occupational safety system.
In the mid-term (starting from 2021), the Company also plans to introduce the ISO 45000:2018 standard to unify working conditions. In order to establish a unified classification of working conditions at workplaces for employees from various enterprises of the holding that perform activities that are similar in terms of their danger, the Company invited a third-party organisation (Klin Institute of Occupational Safety and Conditions). The unification of working condition classes will make it possible, among other things, to optimise the process of providing benefits, compensation, and additional vacation days.
The general principles and requirements of Metalloinvest, which integrate the requirements of all the manuals used, are compiled in corporate documents that describe the Company’s policies on health and safety issues. The corporate documents include:
- Company’s Development Strategy;
- Health, Safety and Environment Policy;
- Major Requirements in Occupational Health and Safety;
- Manager’s HSE Code of Practice.
403-2
In accordance with the requirements of OHSAS 18001:2007, each of the Company’s enterprises has developed a risk and hazard classification system based on which each risk is assigned a level unacceptable or acceptable. Despite the fact that only measures to reduce unacceptable risks are mandatory, the Company also makes maximum efforts to reduce acceptable risks as part of its observance of the principle of permanent risk reduction. All risk reduction measures aim to:
- eliminate sources of danger;
- prevent employees from accessing hazardous areas;
- use safer technical devices, materials, and technologies;
- improve safe work methods and techniques;
- provide visual and automated monitoring of technical parameters that indicate potential danger;
- use locks, alarms, and warning labels;
- reduce the severity of personnel’s exposure to hazards;
- use and improve personal protective equipment.
An assessment of the feasibility of introducing the Integrated System to Ensure Workplace Safety was conducted during the reporting period.
The detailed assessment of the feasibility of introducing the Integrated System to Ensure Workplace Safety identified the advantages and potential difficulties of its integration. Based on the assessment as well as an exchange of experience with representatives of the extractive industry, the Company decided to initiate its own project to automate the management of occupational, industrial and environmental safety issues on the basis of the 1C system.
The distinctive features and advantages of this system are its compatibility with the SAP ERP system in terms of data integration and transmission as well as an interface that is easy to use and accessible for users of any level and is suitable for operational on-site work.
This system will effectively document the results of industrial safety audits. Management will be able to view the data stored in the system, including information on the site at which the audit was conducted, who was designated as the person responsible for eliminating the violations, and when the violations should be eliminated. The system also provides information about the deadlines for eliminating violations, which makes it easier to monitor them. This system is similar to the existing violation log at the Company’s enterprises, although it is fully automated.
Expenditures on Occupational Health and Safety
The Company annually invests in the occupational health and safety of its employees. Total investments during the reporting period amounted to RUB 1,547 million, which were distributed among the following main areas of investment:
- improving the quality and effectiveness of personal protective equipment;
- improving working conditions and sanitary measures;
- increasing the technical level and efficiency of production;
- Enhancing the level of fire safety;
- personnel training and support for training systems.
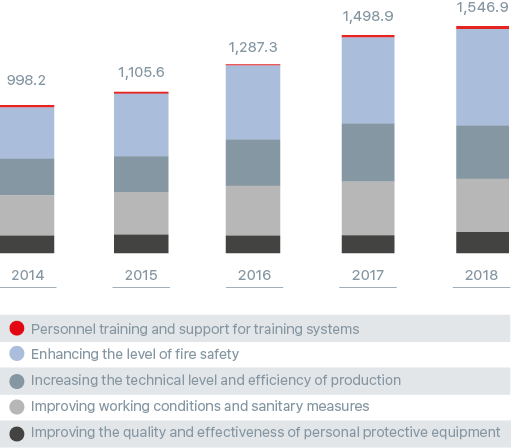
During the reporting period, the biggest increases in investment were seen in the segments Improving the quality and effectiveness of personal protective equipment (10%) and Enhancing the level of fire safety (21%).
2014 | 2015 | 2016 | 2017 | 2018 | |
---|---|---|---|---|---|
Personnel training and support for training systems |
5.1 | 4.3 | 4 | 9.7 | 10 |
Improving the quality and effectiveness of personal protective equipment |
347.1 | 442.2 | 509.2 | 603.8 | 666.1 |
Improving working conditions and sanitary measures |
255.4 | 244.7 | 317 | 399.8 | 365.2 |
Increasing the technical level and efficiency of production |
276.6 | 292.8 | 338.7 | 373 | 369.3 |
Enhancing the level of fire safety | 114 | 121.6 | 118.4 | 112.6 | 136.3 |
Total | 998.2 | 1,105.6 | 1,287.3 | 1,498.9 | 1,546.9 |
Ural Scrap Company is also included in the calculation of indicators related to OHS expenditures.
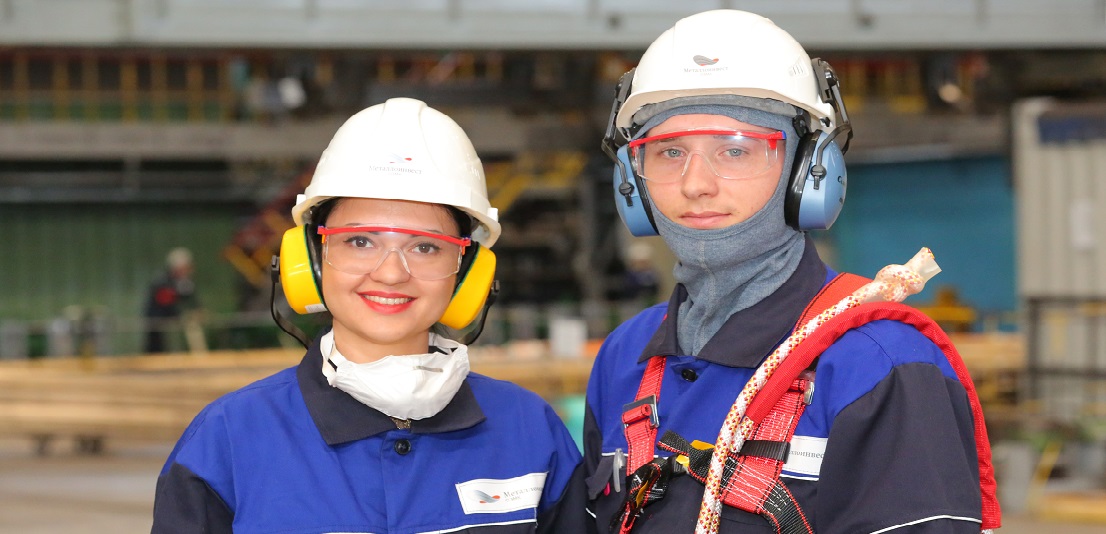
Occupational Injury Prevention
403-2, 403-9
Three fatal accidents took place at the holding’s enterprises during the reporting period. The injury rate (LTIFR) was 0.60. All the accidents that occurred were identified and investigated by a commission chaired by the chief engineer. According to the Company’s requirements, each investigation involves identifying the circumstances, taking pictures, interviewing eyewitnesses and victims, verifying the technical condition of the facility, and complying with OHS requirements. Based on the inspection results, the commission proposes measures to prevent similar accidents (e.g. conducting safety audits, retraining and testing staff on their knowledge about OHS standards, improving the effectiveness of personal protective equipment as well as monitoring and preventive measures) and also conducts an assessment of environmental and material damage.
The injury rate increased compared with the previous reporting period due to the Company’s adoption of a new information transparency policy under which any injury (including microtrauma and off-the-job injuries) must be disclosed and investigated. The investigation procedure is detailed in the new regulation on the investigation of microtraumas, which took effect at all the holding’s enterprises in 2018.
This approach will help to reduce the number of serious injuries going forward since investigating and mitigating any potential danger will ensure the greatest safety of employees.
Moreover, a Stop Card Regulation will be introduced in 2019 in order to ensure employees are as safe as possible. The introduction of the Regulation will result in employees responsible for safety using a special notebook with tear-off stop cards. If a dangerous situation is detected, the responsible employee can prepare a stop card with a full description of the incident that could cause injury to employees and the persons involved. Based on this stop card, work will be suspended at the site, an investigation into the hazardous situation will be launched, and the necessary actions will be taken based on the results of the investigation. This practice is somewhat similar to the Safety Book document that is already used at the enterprises, but it has one key difference. Whereas the previous practice aimed to immediately hold an employee responsible for a violation without conducting an interim investigation, the new practice is more focused on identifying the causes of the hazardous event rather than punitive measures.
At the end of the year, employees who made the greatest contribution to improving safety at the Company’s enterprises – employees who identified the highest number of confirmed violations and employees who ensured the maximum safety in their territory – will be rewarded.
Ural Scrap Company is also included in the calculation of injury indicators.
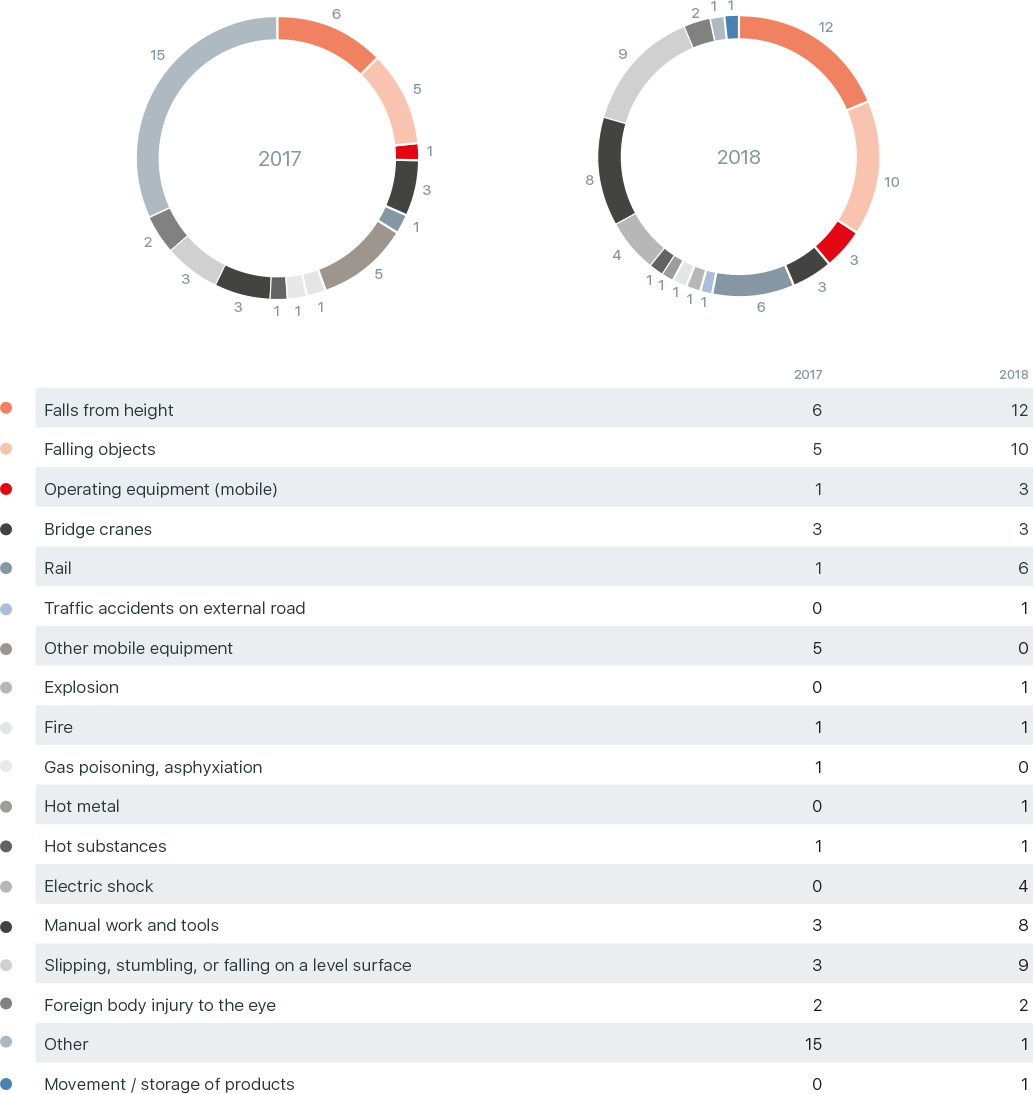
Providing Employees with Protective Equipment in the Workplace
The Company always welcomes feedback on ways to improve OHS, rewards proactive employees, and independently initiates surveys on employee satisfaction with occupational safety. In particular, the Company conducted a survey among employees about their satisfaction with the quality of personal protective equipment (PPE) during the previous reporting period.
The results of this survey were studied and examined in detail in the current reporting period. In particular, based on the results of the previous survey held on 18 May 2018, the Company created the standard Procedure for Testing Pilot PPE, which regulates the testing procedure for industrial prototypes. Per the standard, each piece of PPE that is to be purchased is tested by workers in the workplace for three months. Based on the testing results, employees fill out feedback forms, which are then sent to the commercial service. The test results are among the main criteria for the purchase of the PPE.
In addition, technical specifications for the purchase of PPE that integrate the requirements for the workplace and provide the necessary respiratory and dermatological protection were drawn up during the reporting period. Thus, despite the decentralised purchase of PPE by each individual plant, the requirements for their high quality remain uniform at all the holding’s enterprises.
In the new reporting period, the Company plans to continue testing PPE in the prescribed manner. Employees are to be surveyed again in the second half of 2019.
In addition, workwear will be designed in the same corporate style for all the holding’s enterprises starting from 1 January 2019.
Occupational Safety Training for Employees
403-5
Employees obtain the necessary knowledge about occupational health and safety during training programmes that the Company conducts on a systematic basis. The training programmes meet both the legislative requirements of the Russian Federation as well as the internal standards of the Company’s enterprises. The training programmes cover such issues as occupational safety requirements, occupational risk management, the occupational safety integrated management system, legal support for occupational safety, the rights and duties of employees as regards occupational safety, briefings, social support for workers injured in the workplace, first aid, and environmental safety and offer more than 45 courses in total. Employees have their knowledge on OHS tested through certification and assessments.
Training is conducted by certified health and safety specialists as well as department managers and specialists from the Company’s enterprises both at the Company’s own training centres and at third-party organisations. All training costs are borne by the Company.
In the reporting period, the Company invested more than 350,000 man-hours in training employees of all positions.
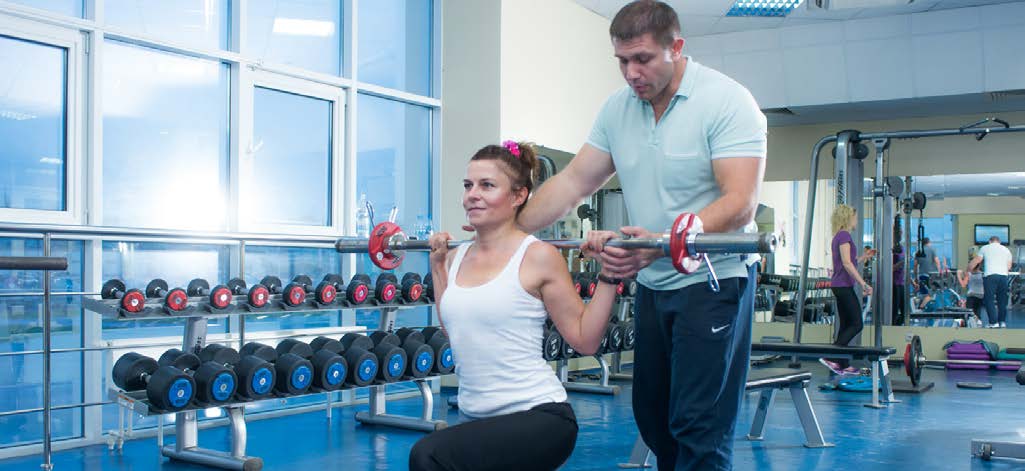
Employee Health
403-1, 403-4, 403-5, 403-6
Metalloinvest continued working on ways to improve the quality of healthcare for employees in 2018. Metalloinvest employees have access to medical services provided by the Company’s clinics and medical centres. At present, corporate medical institutions have a staff of more than 720 employees, including highly qualified medical personnel and support staff. The Company is introducing solutions to automate administrative processes, which has gradually reduced the size of the support staff.
One milestone of the reporting period was that the Company unified the practices of all existing medical services at each of Metalloinvest’s enterprises and the Company’s medical institutions for the first time.
In 2018, the Company worked to harmonise healthcare regulations. This work resulted in the release of the Regulation on Medical Support for the Company’s Employees, which created a cross-functional agenda and distributed responsibility for access to health services among occupational health and safety units as well as social and HR services. Metalloinvest employees were duly informed about the release of the document, which has been publicly available in the internal corporate system since 2019.
56 cases of occupational diseases identified in 2018.
403-10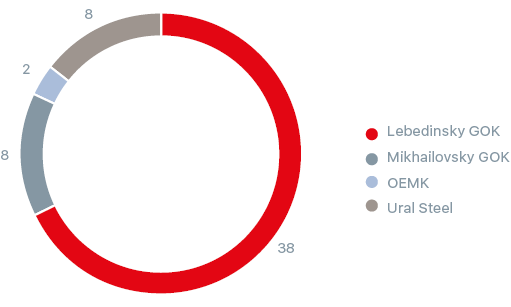
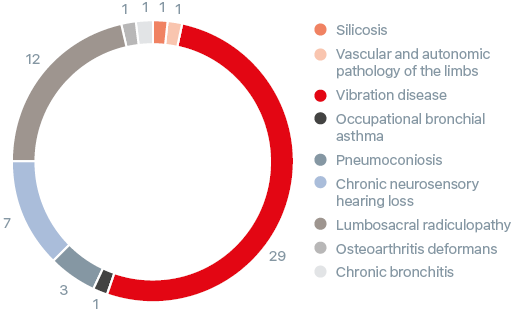
The statistics cover the Company’s employees. The occupational illnesses of third parties (including contractors) are not taken into account.
There was not a single case of occupational illness that resulted in death during the reporting period.
Occupational Illness Reduction Programme
An Occupational Illness Reduction Programme was developed in 2018 based on instructions from the Metalloinvest Board of Directors and is being implemented in collaboration with the Izmerov Occupational Medicine Research Institute. The Programme was launched as part of the Company’s desire to increase the efficiency of medical examinations envisaged by Russian legislation (regulated by Article 213 of the Labour Code of the Russian Federation) given that a substantial proportion of Metalloinvest employees work in harmful and dangerous working conditions.
The Programme not only aims to identify the symptoms of occupational diseases, but to detect early warning signs (signs before the onset of symptoms). This approach is designed to reduce occupational illness as a result of timely diagnosis at the earliest stages. As part of this initiative, the Company invested in the purchase of high-quality medical equipment in 2018 as well as the salaries of healthcare personnel at the Metalloinvest Diagnostic Centre (LebGOK-Health LLC).
In 2018, some 2,000 Lebedinsky GOK employees underwent an examination as part of the pilot launch of the Programme during which it was found that 275 of them had subclinical signs of disease. Preventive measures are being taken for these workers, which will reduce cases of newly diagnosed occupational diseases by 10%. In 2019, the Company plans to continue introducing the initiative at Lebedinsky GOK and also launching the Programme at other Metalloinvest enterprises.
Treatment plans are being developed for employees with signs of occupational diseases. These plans may include outpatient treatment at the day patient facilities of the Metalloinvest Diagnostic Centre as well as health resort treatment at Metalloinvest resorts. The Company has resort facilities in all three regions where it operates: the Ural Health Centre in the Orenburg Region, the Gornyatsky Health Resort in the Kursk Region, and the Belogorye sports complex in the Belgorod Region. In 2018, 7,151 Company's employees underwent a health and wellness programme at corporate and third-party health resorts.
The Company plans to assess the Programme’s effectiveness based on two indicators: the number of cases of occupational disease and the number of new cases of occupational disease that are identified as part of the annual examinations. One of Metalloinvest’s goals in the medium term is to reduce the number of newly detected diseases by 10%, which is a unique KPI on the Russian market among companies in the industry.
In addition to health resorts, the Company is implementing a set of preventive and anti-epidemic measures that aim to reduce the incidence of disease in order to achieve a sufficient level of collective immunity. In particular, it is providing vaccinations for employees. A total of 16,185 employees were vaccinated in preparation for the 2018-2019 flu and SARS season.