Innovations in Occupational Health and Safety
The Company makes enormous efforts to continually improve and modernise the occupational health and safety system.
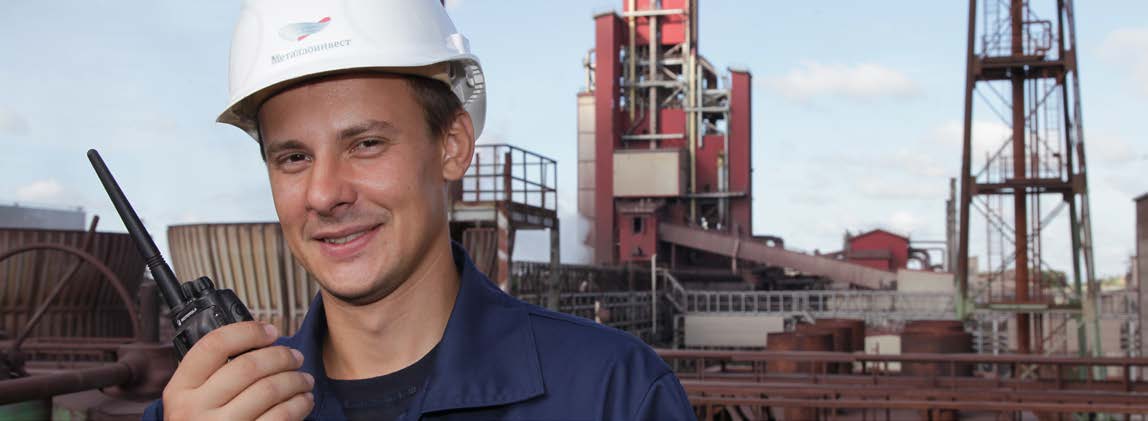
During the reporting period, Metalloinvest considered introducing new technological solutions for the occupational health and safety of its employees in order to improve the effectiveness of existing initiatives and streamline occupational safety management processes. In particular, the Company decided to introduce automated medical examination systems as part of the activities performed by its health centres.
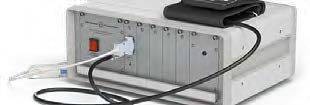
Automated medical examination system
The Company’s health centres continued to function during the reporting period. At present, each of the Company’s enterprises has eight to twelve health centres whose activities include conducting pre-shift medical examinations, including checking employees’ pulse, blood pressure, pupil response, and alcohol levels. Such examinations are particularly important for ensuring the safety of rolling stock workers. In an effort to improve the accuracy of examination results and reduce the human error factor during the diagnosis as well as optimise the work of healthcare personnel, Metalloinvest plans to launch automated examinations in 2019. Technology developed by the System Technologies Group of Companies – one of the leading suppliers of automated occupational safety solutions – provides a comprehensive analysis of a person’s condition (analysis of the pulse wave, hemodynamics, and heart rate), records the examination results, and promptly transmits them to a control panel that is maintained by a medical professional. This solution is expected to help avoid critical errors in the workplace associated with employees’ impaired psychical and physiological condition.
Total investment – RUB 93 million.
As it searches for ways to improve, the Company not only relies on its own expert opinion, but also engages in the practice of exchanging experience with other enterprises, which helps to identify the most effective methods for managing occupational health and safety issues.
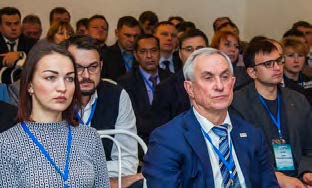
Exchanging experience
Metalloinvest actively developed the practice of exchanging experience to ensure industrial safety during the reporting period and plans to further develop it in 2019.
The Company conducted a series of cross-audits between its enterprises during the reporting period to develop an optimal unified system on industrial safety issues.
In addition to internal exchanges of experience, the Company regularly takes part in external events, including occupational safety measures organised by major mining companies in Russia. The first such event in 2018 for Metalloinvest was the congress ‘Occupational Safety and Ecology at Metallurgical Enterprises’, which was held by MMK PJSC in Magnitogorsk on 12-14 November. In the future reporting period, the Company plans to attend congresses on personal protective equipment issues and other occupational safety and health congresses held by companies in the extractive industry (Gazprom Neft PJSC, Polyus PJSC) and also host its colleagues from the extractive industry.
An exchange of experience resulted in the launch of a project to barcode personal protective equipment. The barcoding procedure involves placing waterproof bar codes on each piece of PPE that contain the owner’s name, information about the employee’s workshop and work section, the issuance date, and the last washing date. During each wash, the data will be scanned so that employees and the responsible parties can be informed when the service life has expired (after more than 20 washes). The project will ensure continuous monitoring of the quality and maintenance of the protective functions of workwear and also prevent its wear.
In addition, experience sharing activities helped identify the need to take a personalised approach to employees in order to improve the occupational health and safety system. In particular, the Company integrated advanced practices for improvements to the OHS culture not only from a technological standpoint, but also in terms of interaction with employees by launching a project that provides internal corporate coaching and conducting behavioural audits during the reporting period. Moreover, as part of the Pursuit of Safety programme, the Company carried out a range of activities with the support of the Corporate Communications Department to visualise dangerous actions and events. The goal of this measure is to provide broad awareness and urge employees to observe safety procedures at their enterprises. Digital posters and slogans, for example ‘They’re waiting for you at home’ and ‘Daddy, come home’, were used as part of the initiative.
Internal corporate coaching system
As part of this project, 14 employees from the Company’s enterprises (foremen and shop floor managers) were trained at the School of Leadership. In an effort to improve its efficiency, the Company eliminated the component of mandatory training and focused on a voluntary initiative. Employees were nominated for training based on their desire to develop a culture of safety among an enterprise’s staff and leadership qualities.
The employees who underwent training later conducted internal corporate industrial safety training sessions in the form of open dialogues and roundtables. Such events take an individual approach taken to each participant and focus on identifying the causes of non-compliance instead of blindly complying with legislative and corporate occupational safety requirements. In 2018, two roundtables were held at each of Metalloinvest’s plants.
The project is expected to result in a significant decrease in the injury rate at all enterprises, which has already been seen at other companies in the industry that have implemented a similar training system. In the future reporting period, the Company plans to double the coaching staff, intensify vocational training, enhance coaching skills, increase the number of events, and expand the audience participating in roundtables
Behavioural safety audits
Behavioural safety audits involving third-party organisations were another measure carried out as part of the Pursuit of Safety programme. The audits aimed to identify the root causes of security breaches using the 5 Whys technique without imposing disciplinary measures. A set of appropriate measures was adopted to reduce workplace injuries based on the results of each of the audits.